Self-tapping screws have revolutionized the construction and manufacturing industries with their ability to fasten various materials without the need for pre-drilled holes. When it comes to securing steel surfaces, understanding the nuances of using self-tapping screws effectively is crucial for achieving optimal results in terms of durability and structural integrity.
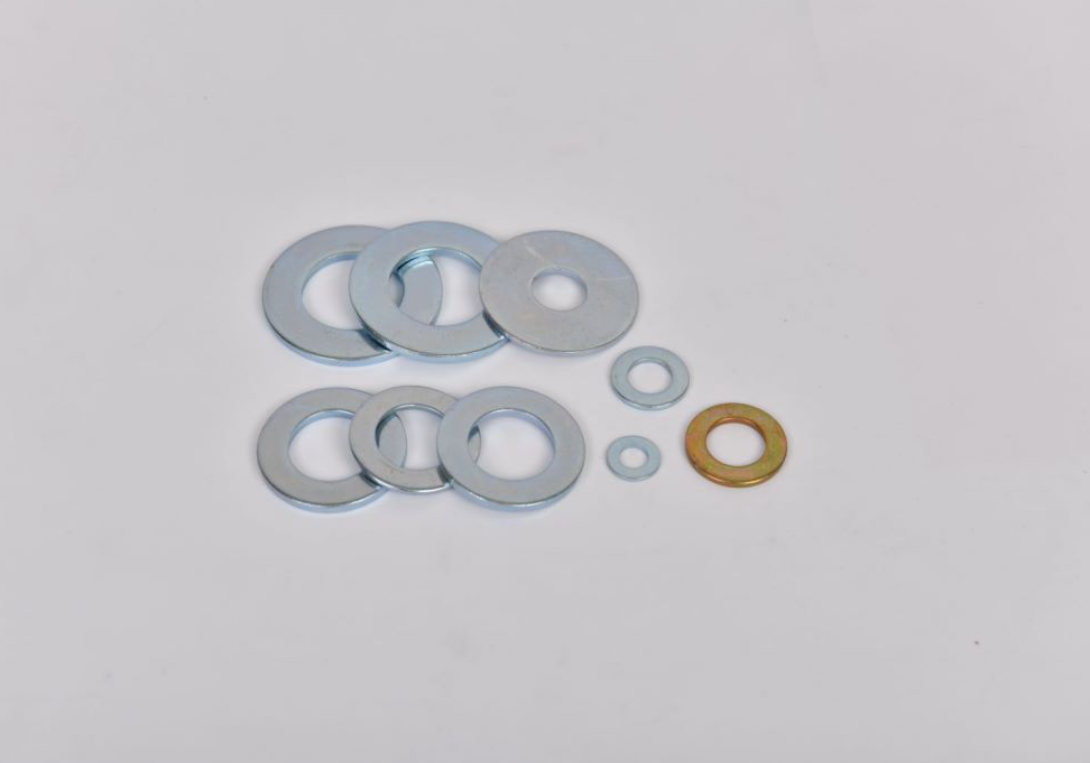
In the realm of construction and metalwork, selecting the correct self-tapping screw is paramount to ensuring that your projects remain secure and resilient over time. The first consideration is the type of steel you are working with, as its thickness and hardness will influence the screw selection process. Self-tapping screws designed for steel are usually made of hardened steel or stainless steel, providing the necessary strength to penetrate this tough material.
An essential factor in using self-tapping screws for steel is choosing the right screw point. For instance, a Type A point is suitable for thinner metals, while a Type B or C point is often preferable for thicker steel, providing a balance between penetration efficiency and grip strength. It is important to note that using an incorrectly matched point type can result in compromised fastening or even damage to the screw or substrate.
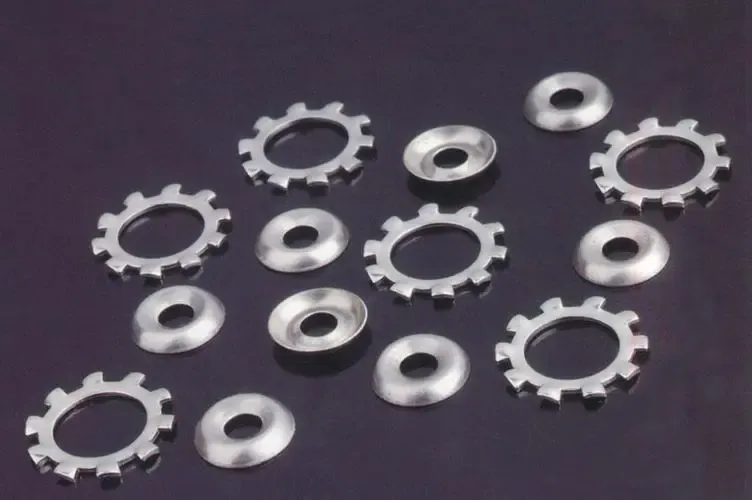
Installation technique is another critical aspect requiring attention. Maintaining an appropriate pressure and speed while driving the screw can significantly impact the effectiveness of the self-tapping process. An overly aggressive approach might strip threads or cause the screw to break, whereas under-driving might not allow the threads to form properly. Utilizing a power drill with an adjustable clutch can aid in controlling these variables, ensuring a more secure and reliable fastening.
One of the advantages of self-tapping screws is their ability to form threads as they are driven into the steel, creating a precisely fitted fastening without pre-drilling. This feature not only saves time but also minimizes the potential for misalignments that can occur with pre-drilled holes. However, for thicker steel, a small pilot hole may still be needed to guide the screw and prevent surface damage, especially when precision is critical.
Ensuring corrosion resistance is essential for projects exposed to the elements or harsh environments. Opt for self-tapping screws with protective coatings, such as zinc-plating or galvanization, to enhance their lifespan and maintain the structural integrity of the fastening. In marine or chemically aggressive environments, stainless steel screws offer a superior option due to their innate resistance to rust and corrosion.
self tapping screw into steel
Another aspect that underscores the effectiveness of a self-tapping screw installation is understanding the load requirements of your project. Determining suitable screw length and diameter relative to the thickness of the steel and weight-bearing demands will ensure a balanced load distribution. Engineers and builders often rely on industry standards and specifications to guide these decisions, ensuring that the selected screws adhere to the necessary safety and performance criteria.
When dealing with steel, precision and preparation go hand in hand. For example, it’s crucial to ensure the steel surface is clean and free of debris before installation. Contaminants can impede the screw's ability to create strong threads, leading to weakened joins. An adherence to clean workspaces is a hallmark of professional craftsmanship, reinforcing trust and authority in structural work.
For manufacturers and construction professionals, the use of self-tapping screws into steel can streamline processes, improve efficiency, and reduce labor costs, providing an innovative solution without compromising quality. This systematic approach enhances both expertise and trustworthiness, building a reputation for reliability and excellence in delivery.
Moreover, advancements in material sciences continue to lead to the development of specialized self-tapping screws designed for even more challenging steel applications. Keeping abreast of these innovations and integrating them into practice not only showcases expertise but also offers an opportunity to provide cutting-edge solutions to clients.
In conclusion, understanding the interplay between screw type, installation technique, and environmental considerations is fundamental to leveraging the full potential of self-tapping screws in steel applications. With the right knowledge and practice, these screws can offer exceptional performance, flexibility, and strength, establishing their status as a cornerstone in modern construction and manufacturing.