Flat washers and spring washers serve as indispensable components in various mechanical applications. Their roles, functionalities, and significance cannot be overstated when it comes to ensuring the integrity and performance of assembled parts. Understanding the nuanced differences between these two types of washers is pivotal for making informed decisions in engineering and maintenance processes.
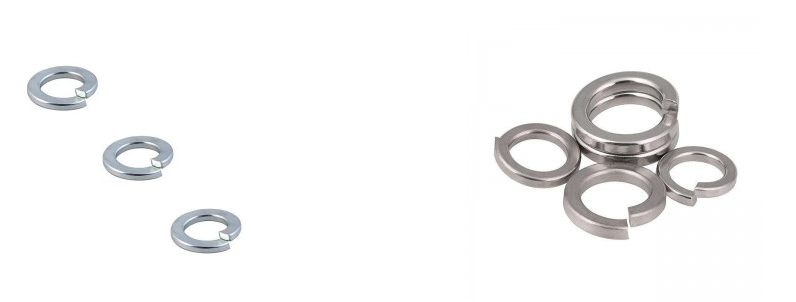
Flat washers, commonly known as plain washers, are typically thin, round disks with a hole in the center. Their primary function lies in distributing the load of a threaded fastener, such as a bolt or screw, across a larger surface area. This distribution helps prevent stress-related damage, such as marring or indentation, on the surfaces being joined. Flat washers also serve to alleviate the friction between the fastener and the surface material, facilitating easier application of torque and achieving more consistent tension.
Spring washers, on the other hand, introduce a level of elasticity and tension that flat washers do not provide. Often referred to as split washers or lock washers, they are designed to prevent fastening loosening due to vibration or dynamic loads. The open-loop structure of most spring washers acts as a compression spring when the fastener is tightened, the washer applies continuous pressure between the head and the substrate. This tension counters any tendency of the nut or bolt to rotate and loosen, thus safeguarding the tightness and reliability of the assembly even in environments subject to constant movement or load changes.
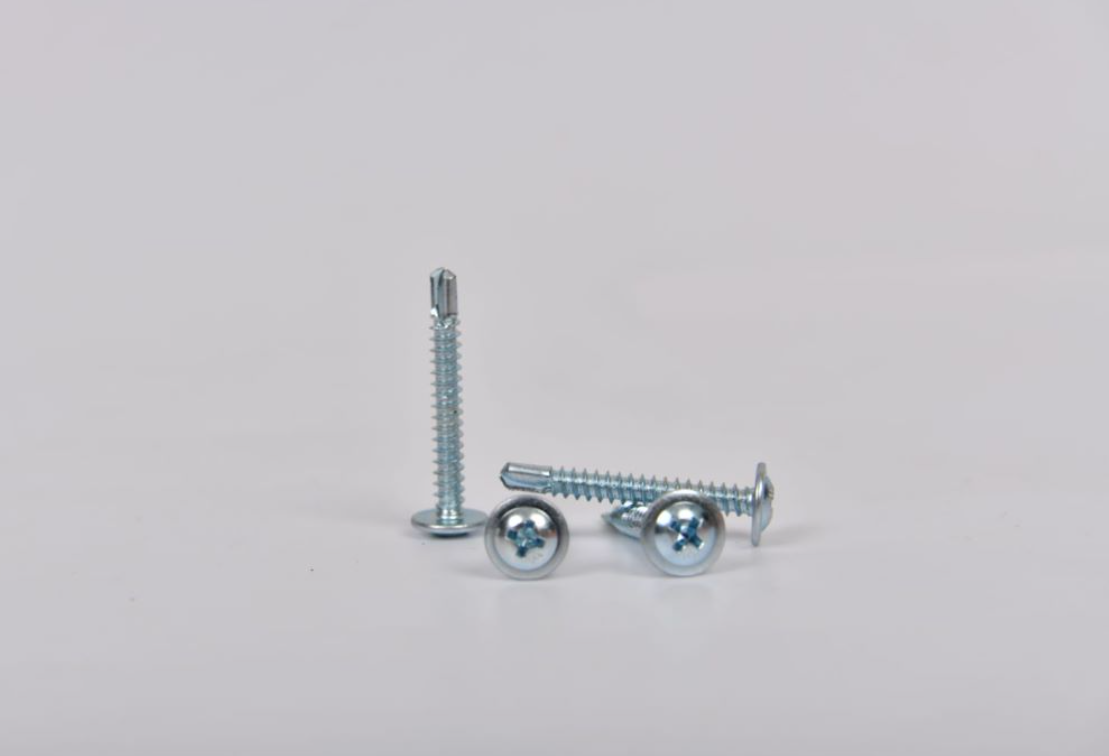
From an engineering perspective, the selection between flat and spring washers transcends mere preference and hinges on application specifics. Flat washers are optimal for distributing forces evenly, which is especially crucial in delicate applications where surface deformation must be avoided. Their simplicity and cost-effectiveness make them an ideal choice in situations where loosening is not a significant risk or where additional locking mechanisms are integrated into the design.
flat washer vs spring washer
Spring washers, with their unique mechanical properties, excel in applications where vibration and thermal expansions could potentially compromise the stability of an assembly. For instance, in automotive, aerospace, or heavy machinery sectors, where equipment is subjected to rapid motion and temperature fluctuations, spring washers are often indispensable. Their ability to maintain pressure within fastened joints ensures structural integrity and reduces the need for frequent maintenance checks for retightening.
When assessing the trustworthiness and reliability of flat versus spring washers, professionals must consider material composition, manufacturing quality, and compliance with industry standards. Stainless steel washers, for example, offer superior resistance to corrosion and are ideal for use in high-humidity or marine environments. Meanwhile, spring washers manufactured with hardened steel or alloy materials can withstand high shear forces and maintain elasticity over prolonged use.
To enforce credibility, engineers and supply chain specialists should verify that washers meet recognized standards such as ISO, DIN, or ASTM. Certification by these bodies confirms that the washers have undergone rigorous testing and validation, ensuring they can withstand the mechanical demands imposed by specific applications. Additionally, consulting with fastening experts and reviewing case studies within the industry can provide invaluable insights into the appropriate choice and application of washers.
In conclusion, flat washers and spring washers each hold distinctive advantages that cater to various mechanical needs. While flat washers are adept at force distribution and protecting surface finishes, spring washers offer reinforcement against vibrational loosening, enhancing the security of bolted joints. Making the correct choice requires a blend of theoretical knowledge and practical experience, taking into account the environmental conditions, load conditions, and maintenance profiles. By relying on expert recommendations and adhering to stringent standards, one can achieve optimal fastening performance that is both reliable and durable across a myriad of applications.