Selecting the right self-tapping screw for your project can significantly influence the success and durability of the assembly. Whether you're working on a DIY project at home or involved in an industrial application, understanding the self-tapping screw size chart in metric measurements is crucial. This comprehensive guide provides valuable insights gathered from extensive experience and technical expertise to help you make informed decisions.
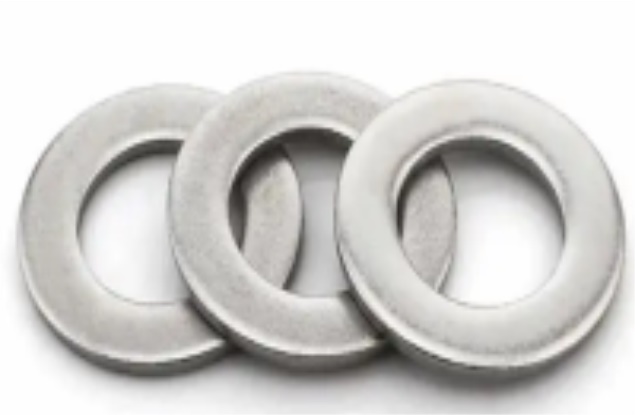
Self-tapping screws are uniquely engineered to tap their own threads into the material as they are driven in. This characteristic makes them indispensable in various applications, especially when working with metals, plastics, and sometimes thinner wood materials. The metric system, widely used in many parts of the world, brings precision and uniformity to the sizing of these screws, which is essential for global applications.
The size of a self-tapping screw is typically indicated by two key measurements the diameter and the length.
Understanding these dimensions in metric units is pivotal. For instance, a screw labeled as M4x25 indicates a screw with a 4mm diameter and a 25mm length. This precise specification helps ensure that the screw is suitable for the desired application, thereby enhancing structural integrity and preventing material damage.
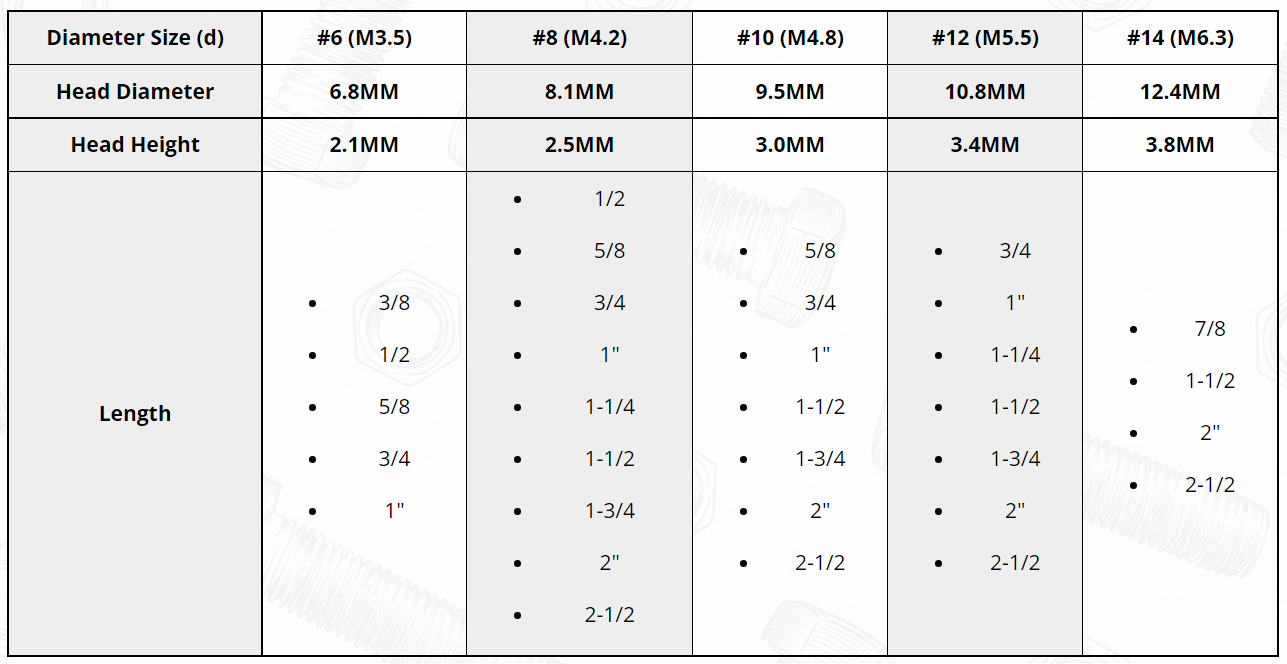
Accuracy in diameter is vital as it ensures the screw fits snugly and forms proper threads in the substrate. A mismatch in the size may lead to improper seating of the screw, resulting in a loose fit or damage to the material, compromising the assembly's integrity. Experience shows that in applications requiring high precision, such as aerospace or medical devices, minute deviations in screw dimensions can have significant repercussions.
Length, on the other hand, determines how deep the screw will penetrate into the material, which is crucial for load-bearing applications. Selecting an appropriate length prevents potential structural failures. For example, in metal framing, using a screw that adequately spans the material thickness ensures a more robust connection which can withstand considerable stress and weight.
self tapping screw size chart metric
In exploring the different self-tapping screw sizes available in the metric system, familiarity with common sizing standards such as ISO or DIN can be advantageous. These standards provide assurances of quality and uniformity, enabling professionals and DIY enthusiasts to rely on these specifications confidently. Moreover, certain projects may mandate adherence to these standards, particularly in regulated industries like construction or automotive sectors.
With expertise comes the understanding of how different materials interact with specific screw sizes and types. Self-tapping screws come in various head styles – countersunk, pan head, and hex head, to name a few – each serving different applications based on aesthetic, structural, or installation requirement considerations. Pairing the right head style with the appropriate size ensures not only functionality but also adherence to design specifications and aesthetic preferences.
Trustworthiness in selecting self-tapping screws also derives from choosing reputable manufacturers and suppliers. High-quality screws manufactured to stringent specifications reduce the risk of project failure. Consulting with industry professionals or engineers can further enhance decision-making, particularly for projects with stringent safety or quality requirements.
In summation, understanding the metric size chart for self-tapping screws is an essential skill that integrates knowledge of mechanical engineering principles, material science, and industry standards. A methodical approach to selecting these screws bolsters project outcomes, ensuring both efficacy and safety. Keeping abreast of evolving technologies and industry trends guarantees that your choices remain at the forefront of innovation and reliability.