For anyone involved in construction, metalworking, or DIY home improvement, self-tapping screws often emerge as an indispensable tool. These screws are amazing for their capability to cut threads into the material they are being driven into. Their utility spans a broad range of applications, including fastening thin metal sheets, joining wood parts, and securing composite materials. Yet, maximizing their potential requires a thorough understanding of their capacity—the ability to handle tensile and shear forces, their material compatibility, and their optimal usage scenarios.
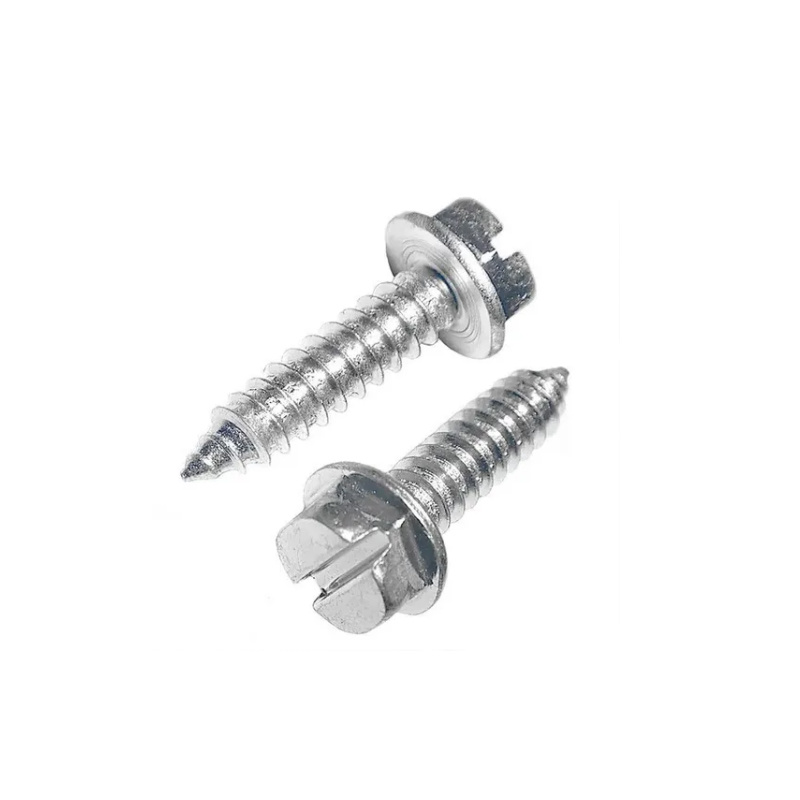
Self-tapping screws are commonly made from hardened steel, stainless steel, or brass, each with specific benefits. Hardened steel variants are widely used because they combine strength with affordability, while stainless steel offers superior resistance to rust and corrosion, making them ideal for outdoor applications or in environments prone to moisture. Understanding the material composition of the self-tapping screw is crucial for gauging its capacity and ensuring it meets the requirements of your project.
The capacity of a self-tapping screw refers to its ability to withstand forces, which is primarily determined by its tensile and shear strengths. Tensile strength is the maximum load a screw can support without breaking when pulled in the direction of its axis, while shear strength is the maximum load a screw can bear without breaking when force is applied perpendicularly to its axis. The dimensions of the screw, primarily its diameter and length, are pivotal in dictating these strength values. A general rule of thumb suggests that the larger the diameter, the higher the capacity, but application nuances and material considerations must not be overlooked.
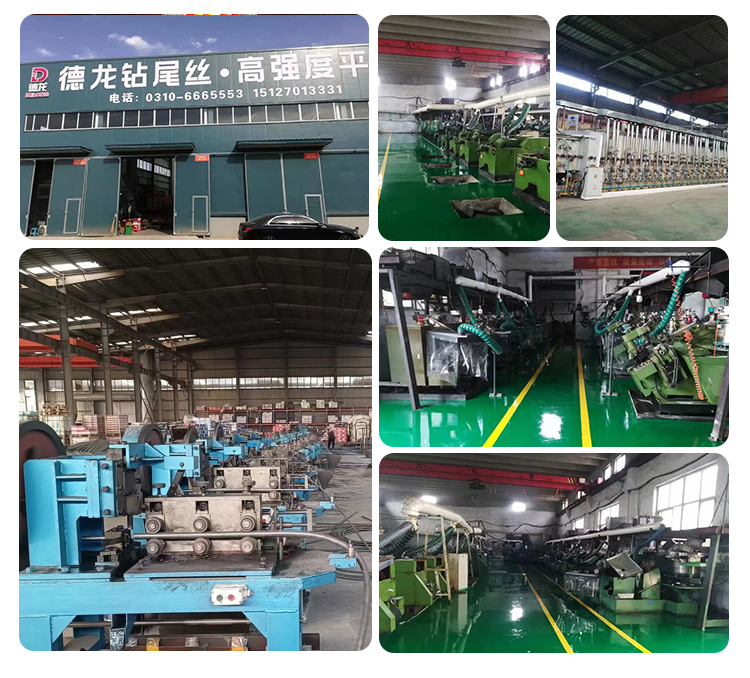
The thread type of self-tapping screws also impacts their capacity. Coarse threads are typically used in softer materials, such as wood or plastics, and are designed to provide a strong grip with fewer rotations. Fine threads are better suited for harder materials like metal, offering greater strength in less material. Ensuring the correct thread type can significantly augment the screw's holding power and durability.
Expertise in selecting the appropriate pilot hole size is another critical factor that directly influences the effectiveness and capacity of a self-tapping screw. A pilot hole that is too small may result in the screw exerting excessive force on the material, potentially leading to cracks or breakage. Conversely, an overly large pilot hole can lead to inefficient thread formation and reduced holding capacity. Ideally, the pilot hole should be slightly smaller than the screw's core diameter to ensure a snug, secure fit while allowing the screw to form its own threads effectively.
self tapping screw capacity
Maintaining the trustworthiness of any project hinges on the consistent reliability of its components, and self-tapping screws are no exception. For high-load or safety-critical applications, manufacturers often provide specifications regarding maximum torque values, recommended burden limits, and optimal driving techniques. Adhering to these guidelines not only maximizes the screw’s functional capacity but also ensures the structural integrity and longevity of the application.
Furthermore, understanding the operating environment is imperative when choosing self-tapping screws. Factors such as exposure to chemicals, temperature extremes, and dynamic loading conditions affect a screw’s longevity and performance. Stainless steel screws are often preferred in harsh environments due to their superior corrosion resistance. Meanwhile, projects involving electrical conductivity or interference may necessitate screws with specialized coatings or platings.
For those seeking to leverage the full capacity of self-tapping screws, regular maintenance and inspection cannot be overlooked. Checking for signs of wear, corrosion, or stress fractures can preempt failures. Moreover, the torque applied during installation should be monitored and controlled, as over-tightening can weaken the material or snap the screw, compromising the entire structure's integrity.
In conclusion, optimizing the contribution of self-tapping screws to a project requires a comprehensive understanding of their material properties, mechanical capacities, and the contexts in which they will be used. By combining this knowledge with precise installation techniques and diligent maintenance practices, one can ensure their trustworthy performance across diverse applications. Such expertise not only safeguards the integrity of the structure but also elevates the overall quality and durability of your work.