When it comes to fastening components in engineering and construction applications, the role of flat washers is often overlooked. However, an M6 flat washer is an indispensable element that enhances the reliability and longevity of your assemblies. Understanding its dimensions and applications can significantly impact project success, efficiency, and durability.
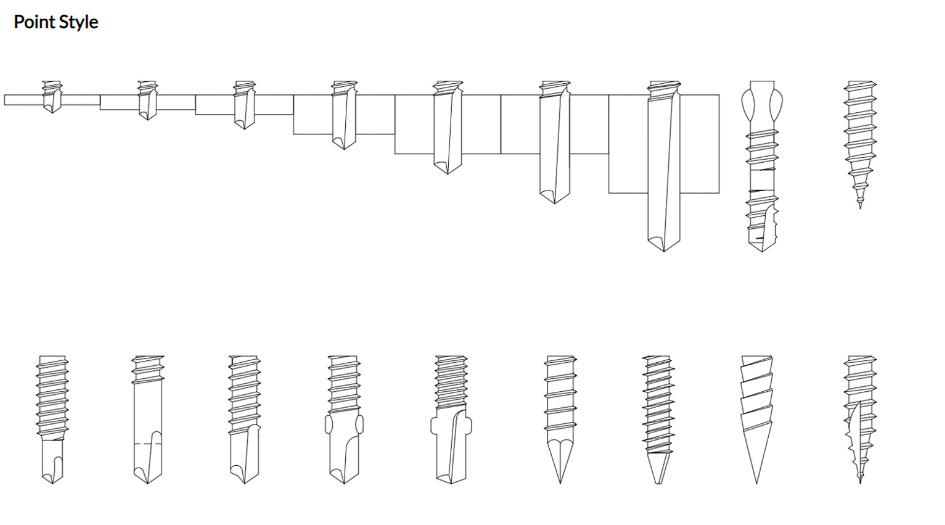
Flat washers, commonly used to distribute the load of threaded fasteners such as bolts and nuts, provide a smooth bearing surface. This distribution of load helps protect the surface being fastened, reducing the risk of damage to the materials involved and helping to prevent loosening over time due to vibrations or dynamic factors. In particular,
the M6 flat washer holds specific appeal due to its versatile dimensions.
The M6 flat washer typically serves Hex bolts and nuts with a Metric thread of 6mm diameter. While actual standards may present slight variations, general M6 flat washers have an inside diameter of approximately 6.4mm to accommodate the M6 bolt comfortably. The outside diameter generally falls between 12mm to 15mm, depending on the series and standard (such as DIN 125, ISO 7089). The thickness can vary, typically falling between 1.6mm to 2mm. The dimensions are crucial not only for mechanical fit but also for ensuring that the washer performs its function effectively—mitigating wear and tear and prolonging the application’s lifespan.
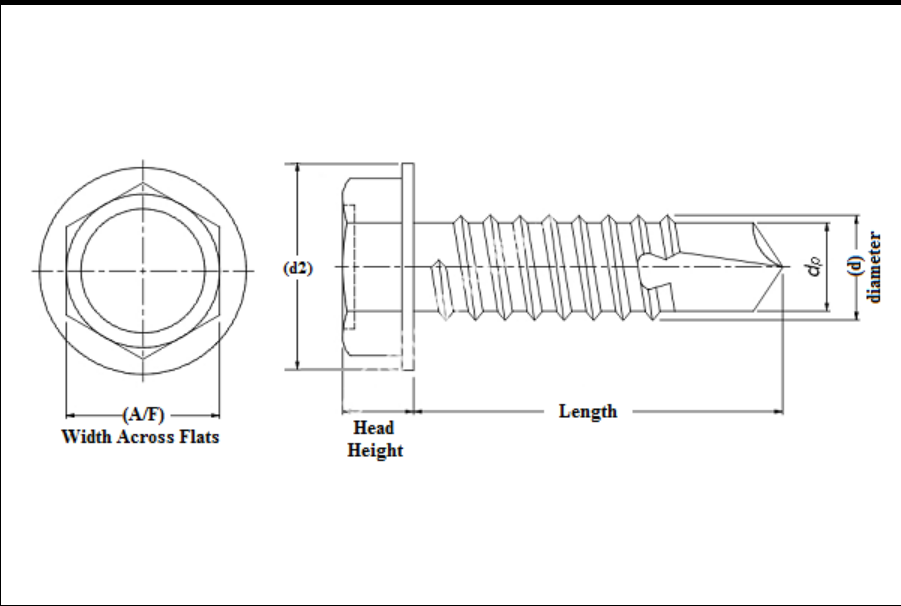
One of the primary reasons for the M6 flat washer’s popularity is its adaptability across various fields. Commonly used in automotive, machinery, communications equipment, and furniture assembly, these washers help to maintain integrity over time. For instance, in automotive applications, M6 washers are often used in engine systems and body panel construction where precision and reliability are crucial.
Selecting the right M6 flat washer involves evaluating several factors beyond basic dimensions. Material choice is paramount; stainless steel, brass, and nylon are popular materials, each bringing different benefits. Stainless steel washers offer superior corrosion resistance and strength, ideal for outdoor or marine environments. Brass, on the other hand, provides excellent thermal and electrical conductivity, making it suitable for electrical applications. Nylon washers offer great chemical resistance and electrical insulation, along with being lighter than metallic options.
m6 flat washer dimensions
Trust in M6 flat washers also hinges on adherence to standards and manufacturing quality. Reputable manufacturers will follow DIN, ISO, or ANSI standards, ensuring consistency and reliability. Always source washers from trusted suppliers who provide certification or documentation of compliance to these standards. This helps create systems your team can trust, minimizing failure rates and ensuring safety.
Installation methods further bolster trustworthiness and reliability. Ensuring that washers are appropriately paired with fasteners and that torque levels are within the manufacturer’s recommended values can bring about significant improvements in system performance. Care and precision during installation prevent the over-tightening that could lead to washer deformation, retainment failure, or damage to the coupled surfaces. Therefore, those responsible for maintenance or assembly should be well-informed of these practical aspects.
The importance of M6 flat washers and their correct application extends beyond simple mechanical function. They ensure safety, improve performance, and contribute to the sustainability of assemblies by reducing the need for frequent maintenance and repair. Their small size and simplicity often belie their critical role in structural and mechanical integrity. Expert knowledge of their dimensions, materials, and appropriate application will enhance the reliability and performance of any project using these fundamental components.
In conclusion, while M6 flat washers may appear to be simple fasteners, their specifics—dimensions, materials, manufacturing quality, and installation—carry significant weight in determining the success of your assemblies. By focusing on these details and adhering to best practices established by authoritative bodies, you ensure not only the functionality but also the long-term reliability and safety of your projects.