Delving into the world of spring washers opens the door to a realm of mechanical innovation that has silently supported countless engineering marvels. These unsung heroes serve as indispensable components that ensure the stability and resilience of mechanical assemblies across a multitude of industries. The diverse array of spring washer types each offers unique characteristics tailored to meet specific application needs.
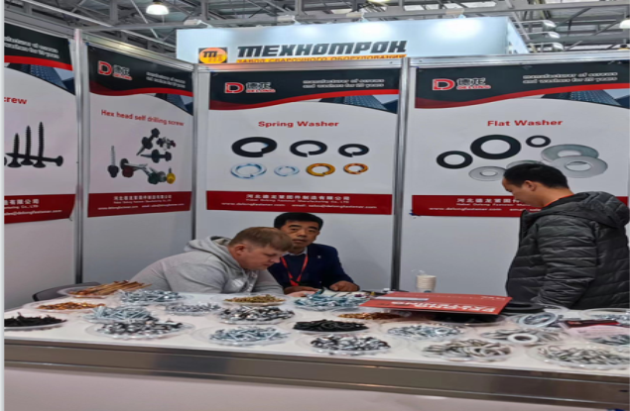
Spring washers, primarily known for providing a preload between two surfaces, play a critical role in maintaining force within a bolted joint. This helps prevent loosening due to vibration, cyclical loading, and thermal expansion. Selecting the right type is crucial for optimal performance, safety, and longevity of the application.
One prevalent type is the Belleville washer, celebrated for its cone-shaped design. This type of spring washer distributes loads evenly and can accommodate axial loads considerably higher than those of flat washers. Thanks to their unique structure, Belleville washers are highly beneficial in thermal expansion situations and settings where space is a constraint. This makes them ideal for applications in aerospace and automotive industries, where precision and reliability are non-negotiable.
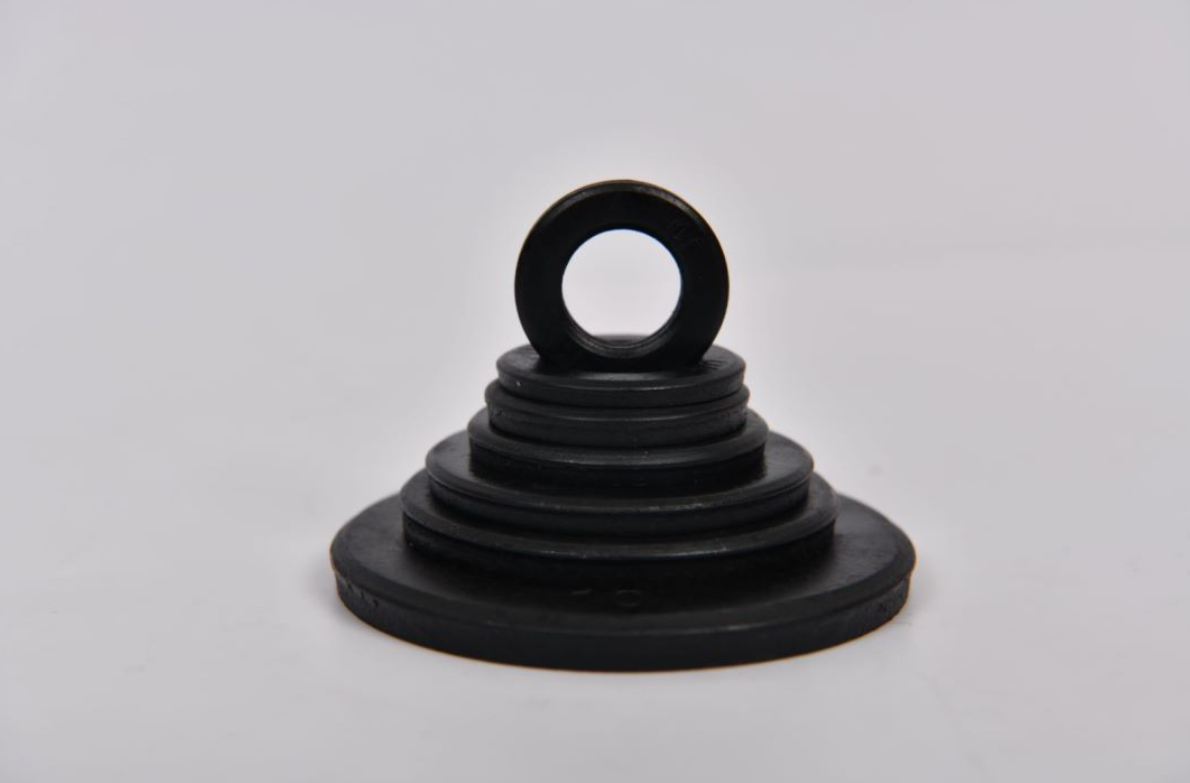
Split washers, or lock washers, are another prominent variety known for their helical shape. They apply a spring force between the bolt and the substrate, minimizing the risk of loosening under load. Split washers are easy to install and cost-effective, often used in general machinery, automotive, and household appliances where moderate vibration protection is essential.
In the realm of electrical engineering and precision instruments, wave washers are a preferred choice. Characterized by their wavy pattern, these washers offer both axial load distribution and the ability to absorb minor vibration, which helps maintain assembly tension. Their flexible nature makes them an excellent fit for maintaining contact pressure in electronic connections, ensuring consistent performance over time.
spring washer types
Tab washers, though less common, provide unparalleled security and reliability. Featuring one or more tabs that lock into place, these washers are instrumental in applications demanding the utmost in safety, such as in heavy machinery and construction equipment. By physically preventing rotation, tab washers effectively complement the overall integrity of the assembly.
Each of these spring washer types reflects a profound understanding of engineering challenges and offers tailored solutions that underscore their indispensability. When considering the implementation of spring washers, it is essential to evaluate factors such as load requirements, environmental conditions, and material compatibility. Balancing these considerations not only enhances performance but also extends the lifespan of the mechanical systems they support.
Furthermore, selecting a high-quality material is vital in ensuring that the washer can endure the environmental stresses it will encounter. Common materials include stainless steel for its corrosion resistance, carbon steel for its strength, and alloys for specialized applications requiring enhanced durability.
Incorporating spring washers into design considerations demands not only technical expertise but also an acute awareness of the specific requirements of the application at hand. Consulting with experts and leveraging industry standards can provide invaluable insights that guide effective choice and application.
Thus, understanding the distinctions and utilities of various spring washer types is imperative for engineers and designers across industries. Their pivotal role in safeguarding mechanical integrity through minimizing risks of loosening and optimizing load distribution distinctly underscores their value. As industries continue to evolve and face new challenges, the adaptability and ingenuity of spring washers remain integral to the development of innovative solutions that push the boundaries of design and functionality.