Self-tapping shoulder screws have become indispensable components across a variety of industries, from automotive and aerospace to consumer electronics and home improvement. Understanding their unique advantages and knowing how to effectively choose and utilize them can significantly boost the performance and longevity of the products they’re used in. This article delves into the essentials of self-tapping shoulder screws, offering expert insights and trustworthy advice.
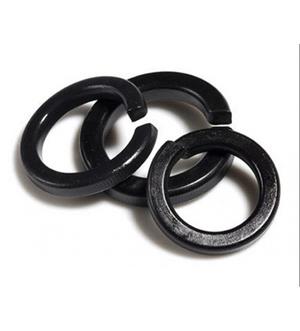
Self-tapping shoulder screws are specifically designed to form threads while being driven into pre-drilled holes. This eliminates the need for a separate tapping tool, saving time and effort during assembly processes. This self-tapping feature makes them particularly ideal for applications involving softer materials like plastics, aluminum, and certain composites where precision and ease of installation are paramount.
One of the defining characteristics of shoulder screws is their design, which includes three major components the head, the shoulder, and the threading. The shoulder section stands out as it provides a smooth surface that can be used as a pivot or bearing surface, perfect for movements or swivels in mechanical assemblies. The length and diameter of the shoulder are critical parameters that need to be matched with the specific application requirements to ensure optimal performance.
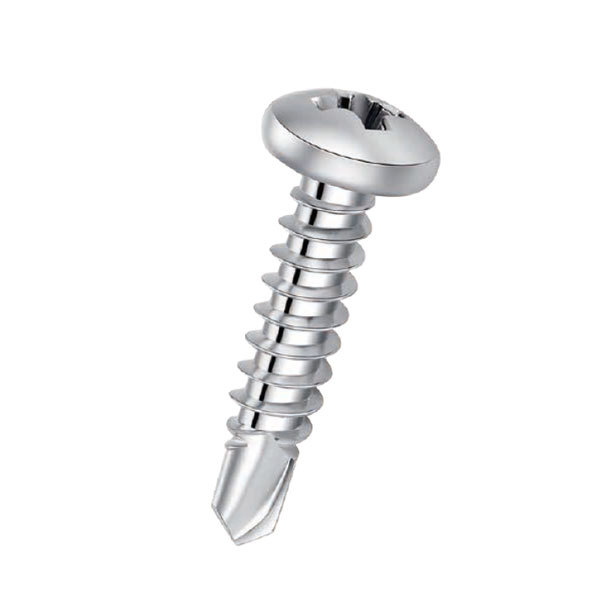
For those working in product design or engineering, the flexibility and reliability of self-tapping shoulder screws can drive significant improvements in assembly processes. Given that these screws cut their own threads, they inherently provide a tighter fit. This reduces the likelihood of loosening due to vibrations or external forces and minimizes maintenance needs post-assembly. Such properties make them a preferred choice in high-vibration environments such as engines or industrial machinery.
The expertise in selecting the right self-tapping shoulder screw hinges on a few key considerations. Material selection is paramount; stainless steel is often recommended for its corrosion-resistant properties, especially in moisture-prone environments. When strength and durability are a priority, hardened steel variants are preferable. Always consider the thermal expansion properties of the material when used in high-heat applications to avoid discrepancies in alignment or stress on the machinery.
self tapping shoulder screw
Trustworthiness in a supplier is essential. Always source self-tapping shoulder screws from reputable manufacturers who provide clear specifications and consistently high-quality products. Certifications such as ISO 9001 can offer assurance of manufacturing quality and process integrity. Additionally, platforms like customer reviews and industry-specific testimonials can further enhance trust in a supplier.
Experience in the logistics of utilizing self-tapping shoulder screws indicates that proper installation is critical to leveraging their full benefits. Over-torquing can strip the material being fastened, especially in softer substrates, while under-torquing may fail to achieve the necessary holding power. Proper training in torque application and using the right tools and fastening equipment are advised.
Another often overlooked aspect is the environmental impact of materials, which speaks to the sustainability criteria increasingly considered in manufacturing. Opting for recyclable or sustainably sourced materials can align with green initiatives and appeal to environmentally conscious consumers.
Future trends in self-tapping shoulder screws are geared toward innovations in materials and designs that enhance efficiency and reduce costs. Advancements in metallurgy and coatings that increase frictional grip and reduce galling are on the horizon, as is the integration with digital tracking for quality assurance in supply chains.
In conclusion, self-tapping shoulder screws offer exceptional functionality for a wide range of applications due to their self-sufficiency in threading and inherent reliability. Their design is perfect for applications that require pivoting or rotational movements without compromising on structural integrity. Emphasizing expertise, authoritativeness, and trustworthiness in handling these versatile fasteners can dramatically enhance product quality and operational efficiency.