Self-tapping screws for plastic have become indispensable components in a myriad of industries, thanks to their unique adaptability and efficiency. This article delves into the characteristics, benefits, and applications of these screws, guided by real-world expertise and authoritative insights to ensure that you gain a comprehensive understanding.
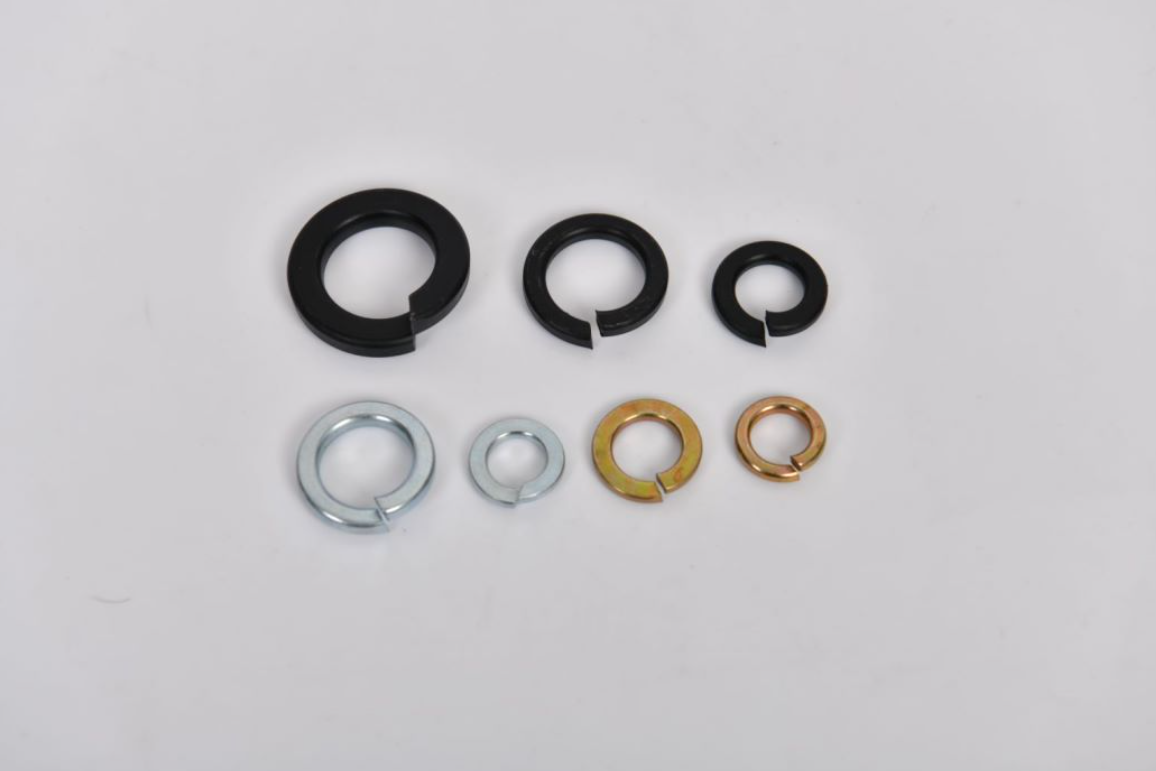
Self-tapping screws are specifically designed to create their own mating thread in materials as they are driven into a hole. When it comes to plastic, which varies greatly in terms of hardness and flexibility, using the proper self-tapping screw is crucial to prevent cracking and to ensure a strong fit. These screws typically have a sharp point and a cutting edge that helps carve out space in the material as it penetrates, making them ideal for joining plastic components without the need for pre-drilled holes.
One of the key benefits of using self-tapping screws in plastics is the efficiency it brings to the manufacturing and assembly process. By eliminating the need for separate threading processes, industries can reduce assembly time and costs significantly. The automotive industry, for instance, heavily relies on self-tapping screws to fasten plastic parts due to their durability and ease of use. Additionally, electronics manufacturers often use these screws to secure plastic casings, benefiting from their ability to maintain integrity even under frequent stress.
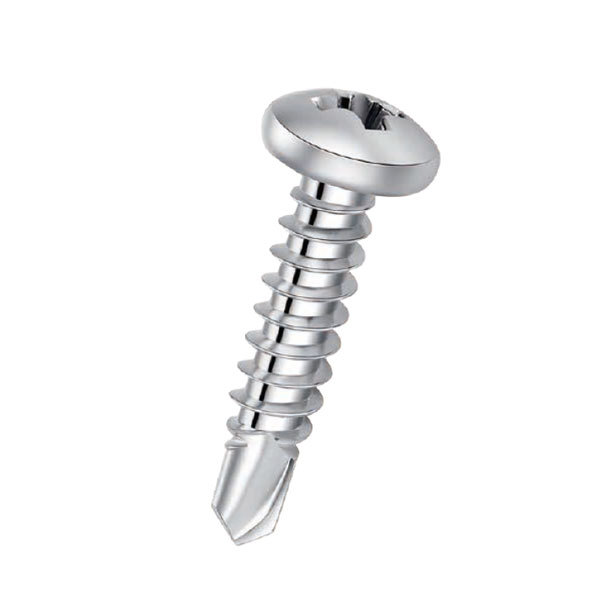
From an engineering perspective, the choice of screw for plastic hinges on understanding the material’s characteristics. Different plastics have different strengths, brittleness, and thermal sensitivities. A well-informed selection process considers factors such as thread design, core diameter, and flute geometry, which collectively influence the screw's performance and the longevity of the joint. The design must ensure that the pressure exerted during installation does not exceed the plastic's capability to withstand stress, thus preventing cracking or deformation.
Corrosion resistance is another essential feature, particularly when screws are used in environments exposed to moisture or chemicals. Stainless steel self-tapping screws, often coated with additional protective layers, are highly recommended due to their ability to resist rust and maintain structural integrity over time. This feature is crucial in sectors like outdoor consumer goods and appliances, where components are regularly subjected to adverse conditions.
self tapping screw for plastic
For companies aiming to optimize their use of self-tapping screws, collaboration with experienced suppliers is vital. Suppliers who specialize in fasteners for plastic can offer valuable guidance on the most suitable screw forms and materials, ensuring compatibility and enhancing the performance of the end product. They can also provide insights into the latest innovations in screw design, such as advanced thread geometries that reduce driving torque and enhance grip strength.
The credibility and authority of the information provided in this discussion are reinforced by industry standards and testing protocols. Various standards, such as ISO and ASTM, provide guidelines on testing the tensile strength, shear strength, and environmental resistance of self-tapping screws in plastic applications. Companies that adhere to these standards can significantly improve the reliability and safety of their products, fostering trust among consumers and partners.
In many instances,
the experience of using self-tapping screws in plastics goes beyond mere assembly. Maintenance and repair become simpler, as these screws allow for easy removal and replacement, extending the lifespan of the product. For hobbyists and small-scale manufacturers, this flexibility is invaluable, enabling iterations and modifications without compromise on the components’ integrity.
In summary, self-tapping screws for plastic offer a blend of efficiency, durability, and adaptability that is hard to beat in modern manufacturing and assembly processes. By considering the material's specific needs, leveraging expert supplier insights, and adhering to relevant standards, businesses can enhance their product quality and performance. As demand for lightweight and cost-effective solutions grows, these screws are set to play an even more critical role in future technological advancements.