Understanding the proper order of installing spring washers and flat washers can significantly enhance the performance and longevity of your machinery or construction project. As washers play a critical role in load distribution and preventing bolt loosening, their correct order is essential. Below, we delve into expert insights and practical experiences to guide you on this topic.
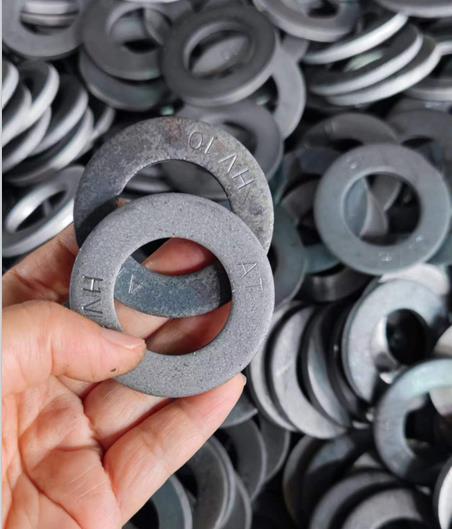
In most mechanical applications, understanding the purpose of each washer type is crucial. Flat washers, often termed as plain washers, serve the primary function of distributing the load of a threaded fastener. They act as a consistent surface area for the nut or the bolt head, preventing the marring of the assembly surface and ensuring the force is spread evenly over a larger area.
Spring washers, often referred to as lock washers, are designed to prevent bolts from loosening due to vibration and dynamic loads. They achieve this through their unique shape, which exerts continuous force onto the bolt's surface, maintaining tension and minimizing the risk of the fastener backing out.
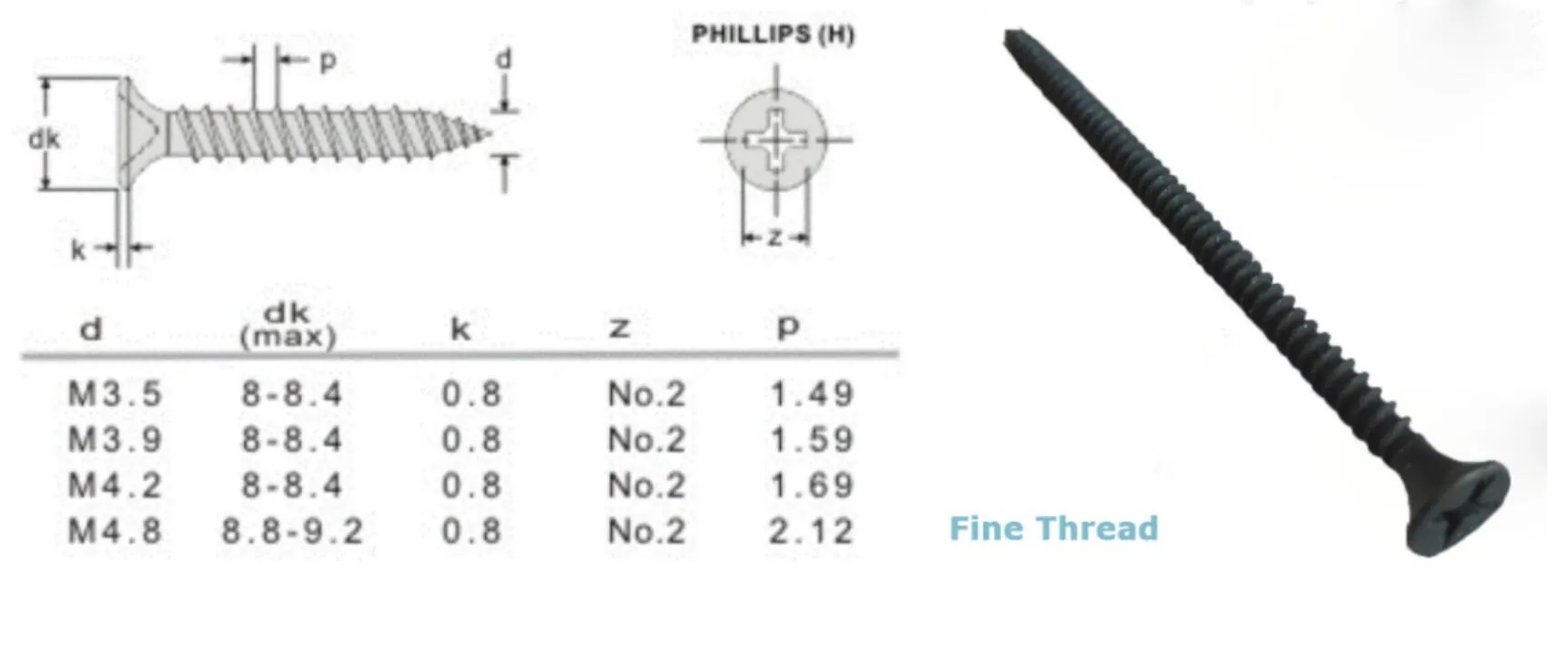
For an authoritative installation process, many industry experts recommend placing the flat washer directly against the surface of the material being fastened. This approach ensures the load is evenly distributed across the surface, safeguarding the integrity of the material. The flat washer also acts as a protective barrier that minimizes potential damage to the material's surface from the turning bolt or nut.
After positioning the flat washer, the spring washer should be placed between the flat washer and the nut or bolt head. This arrangement allows the spring washer to exert its tensioning force effectively, providing an optimal locking mechanism to counteract loosening forces such as vibrations or changes in load.
In professional practice, the specific combination and order may vary based on the application and the environment in which the fastener will be used. For instance, in high-vibration environments, such as within engines or heavy machinery, the effectiveness of the spring washer becomes paramount. Experienced engineers might choose to double the washers or use specialized variations that cater to specific needs.
order of spring washer and flat washer
Testing and feedback from field applications underscore the importance of selecting washers made from appropriate materials. For environments exposed to corrosive elements or high moisture, stainless steel or coated washers are advised to prevent rust and degradation, which can compromise the fastener's performance. Personal accounts from experienced builders and engineers highlight successful projects that owe their durability to the careful selection and ordering of washers.
Authoritative texts on mechanical assembly stress the importance of adhering to manufacturer guidelines. These offer specific insights into the preferred washer types and configurations for different applications, ensuring safety and optimal functionality.
Anecdotal experiences shared within industry networks often provide practical tips for challenging scenarios. One such tip is the combined use of both external and internal tooth lock washers alongside flat washers for maximum hold in particularly demanding applications. This approach, although slightly unconventional, has proven effective in preventing loosening in cases such as automotive assembly or heavy-duty manufacturing.
It's vital that engineers and assembly technicians validate their washer configurations through testing, especially when employing them in new or unique applications. This ensures the configuration's reliability under anticipated conditions and compliance with relevant industry standards and regulations.
Ultimately,
the correct order and combination of spring washers and flat washers lead to improved mechanical reliability and longevity. As with any engineering decision, the chosen approach should be informed by a deep understanding of the fastener's operating environment, a meticulous analysis of potential loads, and a robust adherence to best practices as dictated by industry leaders.
Trusted sources like bolt and washer manufacturers, standardized engineering handbooks, and peer insights remain invaluable for making informed choices. They ensure that every aspect, from material selection to washer order, contributes to the overall safety and success of a project.