The evolution of machine screws, particularly of the self-tapping variety, has revolutionized the way industries approach fastenings in manufacturing and construction. At the heart of this innovation lies the 10-32 self-tapping machine screw, a technological marvel that embodies both efficiency and precision.
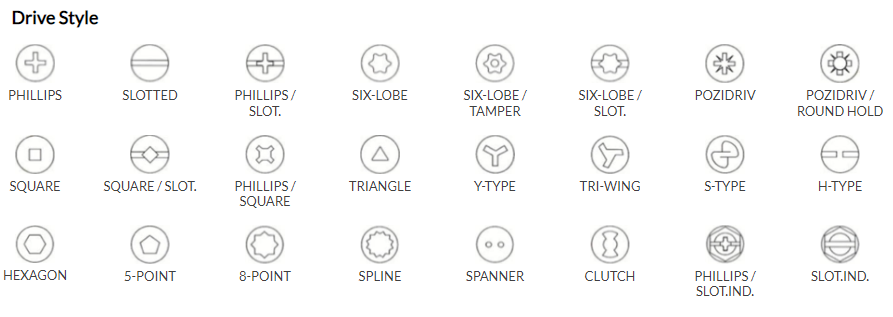
Renowned for their adaptability, 10-32 self-tapping machine screws are engineered to cut their own threads into materials, eliminating the need for pre-drilled pilot holes. This self-starting feature significantly reduces assembly time and labor costs, enhancing productivity in both industrial and DIY projects. Imagine the transformative impact on assembly lines, where time is literally money; these screws streamline operations, offering manufacturers a competitive edge in fast-paced markets.
The dimension specification 10-32 speaks volumes about its versatility. The “10” denotes the size of the screw, while “32” indicates the thread count per inch. This specific configuration offers a balance of strength and ease of use, making it ideal for applications requiring robust fastening with minimal effort. It’s the go-to choice in scenarios where components need secure, efficient, and reliable assembly - from electronics enclosures to metal and wood constructions.
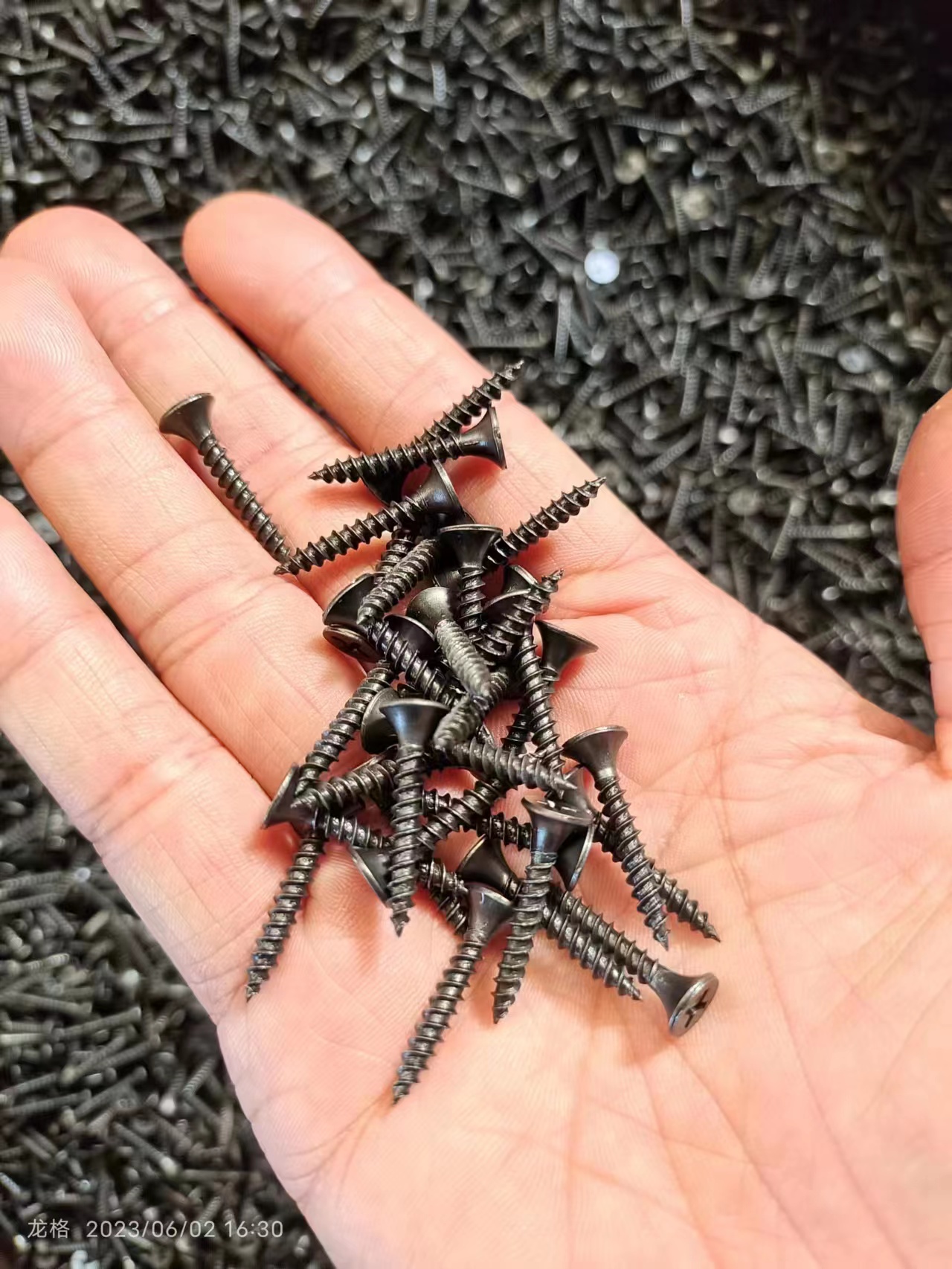
Expertise in utilizing 10-32 self-tapping machine screws starts with selecting the right material. Whether crafted from stainless steel, brass, or carbon steel, these screws can be tailored based on specific environmental conditions and mechanical demands. Stainless steel variants are preferred for their corrosion resistance, perfect for marine or outdoor applications. In contrast, brass self-tappers are ideal for scenarios demanding aesthetic finesse alongside functionality, especially in architecture and design projects.
10-32 self tapping machine screw
Professional application of these screws requires an understanding of the substrate material. For maximum effectiveness, they must match the material’s hardness to avoid striping or fracturing. An expert knows that using the right torque is crucial to prevent over-tightening, which can compromise the structural integrity of the screw and the joined materials. Trust in such small components builds the framework for larger, dependable structures.
Authoritative figures in fastener technology often recommend 10-32 self-tapping screws for projects that encompass both automation and manual assembly. They are favored in precision-driven industries such as automotive manufacturing and aerospace, where every component must adhere to stringent quality standards. Here, engineers leverage these screws not only for their mechanical strength but also for their reliability and ease of inspection, proving indispensable during both assembly and maintenance phases.
Trustworthiness of these fasteners is established through rigorous testing and compliance with international standards. Manufacturers subject them to extensive quality checks involving tensile strength assays, stress testing under various conditions, and corrosion resistance evaluations. This certifies that the screws can withstand operational stresses while maintaining their mechanical properties over time.
In a landscape where innovation and efficiency drive success, the 10-32 self-tapping machine screw emerges as a pivotal tool. It empowers industries with not merely a component of construction but a cornerstone of modern engineering solutions. From experts who innovate new applications to businesses that incorporate them into everyday use, the journey of these screws is marked by a blend of experience, expertise, authoritativeness, and trustworthiness. Whether constructing skyscrapers or assembling cutting-edge gadgets, the 10-32 self-tapping machine screw remains a testament to human ingenuity in solving complex fastening challenges with simplicity and efficacy.